POLYTONE®
Phenol Formaldehyde and Phenolic Resin

About POLYTONE® AP & PF SERIES -PHENOLIC RESINS
Polyols & Polymers Pvt. Ltd. via its POLYTONE® range of resins offers a broad range of technical resins specifically designed for the needs of manufacturing of paints, coatings, varnishes, inks, cable insulation, wire enamels, can coatings, epoxy diluents etc.
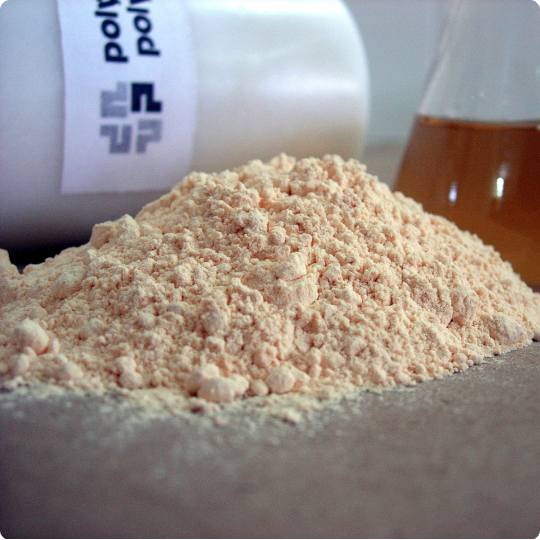
POLYTONE® |
Wire Enamel
|
Cable Insulation
|
Paints
|
Inks & Varnish
|
Antifreeze Polyamide Inks
|
Spar Coatings Weather
Resistant
|
Epoxy Diluents Can Coatings
|
Thermoplastic
|
Thermosetting
|
Composites Refractory
|
Abrasives Emry Wheels
|
Contact Adhesive Rubber
Adhesive
|
|
---|---|---|---|---|---|---|---|---|---|---|---|---|---|
AP 108 EL | PtBP Resol | ✔ | ✔ | ✔ | ✔ | ✔ | |||||||
AP 109 EL | PtBP Resol | ✔ | ✔ | ✔ | ✔ | ✔ | |||||||
AP 110 EL | PtBP Resol | ✔ | ✔ | ✔ | ✔ | ✔ | |||||||
AP 120 E | PtBP Novolak | ✔ | ✔ | ✔ | ✔ | ✔ | ✔ | ||||||
AP 1201 E | PtBP Novolak | ✔ | ✔ | ✔ | ✔ | ✔ | ✔ | ||||||
PF 132 | PF Novolak | ✔ | ✔ | ✔ | ✔ | ✔ | |||||||
PF 420 | PF Novolak | ✔ | ✔ | ✔ | |||||||||
PF 425 | PF Novolak | ✔ | ✔ | ✔ | |||||||||
PF 200 | 2 Part PF Novolak | ✔ | ✔ | ✔ | |||||||||
PF 201 | 2 Part PF Novolak | ✔ | ✔ | ✔ |
Properties
Product Name POLYTONE® | Thermoset | Thermoplastic | Alkyl Phenol Based | Pure Phenol Based | 2 Component |
---|---|---|---|---|---|
AP 108/9/10 EL | ✔ | ✔ | |||
AP 120E/1201E | ✔ | ✔ | |||
AP 132/PF 132 | ✔ | ✔ | |||
PF 420/425 | ✔ | ✔ | |||
PF 200/201 | 2 Component | ✔ + Catalyst |
Type
Heat Reactive/Reactive
Alkylphenol Formaldehye
Chemistry POLYTONE® AP 108/109/110 EL
Thermosetting
PtBP Formaldehye
PtBP Resin
Tert Butyl Phenol
Toluene Free
Phenolic Resin Type
Resol
Resole
Non Reactive Thermoplastic Pure Phenolic Resins
Type
Non Heat Reactive
Thermoplastic
Chemistry : POLYTONE® AP 120E/AP 1201E
Alkyl Phenol Formaldehyde
PtBP Resin/Butyl Phenol
Para Tert Butyl Phenol Resin
Chemistry: POLYTONE® AP 132/ 1321/PF 132/PF 420/PF 425
Phenol Formaldehdye
Unmodified Phenolic Novolak
Chemistry: POLYTONE® PF 200/201
2 Component Phenol Formaldehyde Resin
Moulding Powder
Phenolic Resin Type
Novolak
Heat Reactive Thermosetting Phenolic Resins
The addition of high heat resistance POLYTONE® AP 108/109/110 substantially increases adhesion to substrate. It helps lower initial viscosity and hence improves flow ability of formulation. Because of its reactivity, adhesion properties and heat resistant it has also found application in varnishes, insulation coatings, printing inks.
Can be used in formulation of hard ink resins and coating with chemical resistance. In formulation of medium & long oil exterior and interrior varnishes and spar varnises for deck and floor.
Alkyl Phenol Resins/Speciality Grades/Heat Resistant Grades | |||
---|---|---|---|
POLYTONE® AP 108 EL | POLYTONE® AP 109 EL | POLYTONE® AP 110 EL | |
Chemical Classifiction | Butyl Phenol (PtBP) Formaldehyde Resol Resin | ||
Color (Gardner) 60% in Toluene | 6 MAX | 6 MAX | 6 MAX |
Softening Point (Ball & Ring) | 110°C – 125 °C | 95°C – 110 °C | 110°C – 120 °C |
Melting Point (Capillary) | 75°C – 90 °C | ||
Viscosity (B4 Ford Cup @ 30°C) | 80°C – 130 Sec (60% Soln in Toluene) | 35 – 70 Sec (60% Soln in Toluene) | 35 – 75 Sec (60% Soln in Toluene) |
Methylol Content | 8 – 13 % | 10 – 14 % | 10 – 14 % |
Moisture Content | ≤ 0.5 % | ≤ 0.5 % | ≤ 0.5 % |
Characteristics |
|
|
|
Solubility | Resins are soluble in aromatic hydrocarbon solvents , chlorinated hydrocarbons , ketones and esters etc. | ||
Application/Industry | Formulation of inks with chemical resistance. Medium and long oil exterior oil varnishes and spar coatings Manufacture of coil coatings, cable insulation and high-performance coatings Manufacture of polychloroprene rubber adhesives with high heat resistance. |
Suggested Formulation for High Performance Coating
Component | Ratio |
---|---|
Solvent | 100 Parts |
Polyester Polyester Imide |
25 – 35 Part |
Polyamide Imide | |
Stabilizer | 1-2 Parts |
Anti oxidant | 1-2 Parts |
POLYTONE® AP 108/109/110 | 4-5 Parts |
Non-Reactive Thermoplastic Pure Phenolic Resins
POLYTONE® AP 1201 E and AP 120 E are a non heat reactive thermoplastic phenolic resin with excellent alcohol.
It is quick drying, has excellent color retention and is resistant to weathering, alkalis, water and abrasion. It is designed to develop high tack levels in rubber compounds which are used in tyre construction and mechanical goods.
POLYTONE® AP 1201 E and AP 120 E finds its use in tung-oil based varnishes processed at 450°C.
POLYTONE® AP 1201 E and AP 120 E will add surface harness to polyamide-based inks.
Phenolic Resins /Tackifier / Tackifying/Insulating/Anti-Freeze For Flexo Ink | |||
---|---|---|---|
POLYTONE® AP 1201 E | POLYTONE® AP 120 E | ||
Chemical Classification | Pure Phenolic Resin (Novolak) | Pure Phenolic Resin (Novolak) | |
Type | Non Heat Reactive /Tackifying Thermoplastic | Non Heat Reactive /Tackifying Thermoplastic | |
Colour | Light Reddish Brown | Pale Yellow/Light Reddish Brown | |
Colour Gardner (60% Soln in Xylene) | 12 Max | 8 Max | |
Softening Point (Ball & Ring) | 135 – 145 °C | 150 – 165 °C | |
Acid Value | 100 mg KOH/ g resin (Max) | 1100 mg KOH/ g resin (Max) | |
Characteristics |
|
||
Solubility | These are oil soluble phenolic resin. It has complete solubility in all vegetable oils, aromatics, ketones soluble in esters, ketones, aromatic and aliphatic chlorinated hydrocarbons. oil It has limited solubility in aliphatic. Insoluble in alcohols. | ||
Benefits | Excellent compatibility in synthetic and natural rubbers. Blends easily into rubber stocks These shall provide resistance against weather, alkali, water and abrasion | ||
Application/ Industry | Tyre /Tire Building, Conveyor Belts, Rubber Hose, Rubber Lining, Rubber Mats, Rubber Sheets, Reinforced Rubber, Fabric Lined Rubber, Rubber Adhesives. Weather resistant finishes, Spar Varnishes, Cold-Mix Varnishes |
Non-Reactive Thermoplastic Phenol Formaldehyde Resins
Non-Reactive Thermoplastic Phenol Formaldehyde Resins
POLYTONE® Resins which are on unmodified phenols provides higher hardness compared to other products
They are designed to give a consistent performance as a reinforcing or binder or base resin. There are used as a reinforcing resin in tire beads, shoe soles, apex strips and co-extruded window profiles
POLYTONE® PF 132 can be used as an epoxy-phenolic co reactant in wide range of epoxy co reactant applications like laminates, adhesives and coatings
POLYTONE® PF 132 can also be used in varnishes, insulations, inks and coatings
Phenolic Resins /Binder/ Reinforcing | |||
---|---|---|---|
POLYTONE® AP 132 | POLYTONE® AP 1321 | POLYTONE® PF 132 | |
Chemical Classification | Phenol Formaldehyde Resin (Novolak) | Phenol Formaldehyde Resin (Novolak) | Phenol Formaldehyde Resin (Novolak) |
Type | Non Heat Reactive / Thermoplastic | Non Heat Reactive / Thermoplastic | Non Heat Reactive / Thermoplastic |
Colour | Pale Yellow/light Reddish Brown | Pale Yellow/light Reddish Brown | Pale Yellow/light Reddish Brown |
Softening Point (Ball & Ring) | 110 – 116 °C | 90 – 100 °C | 100 – 116 °C |
Methylol Content | - | 1.0% Max | - |
Free Phenol | 1.0% Max | 1.0% Max | 0.50% Max |
Ash Content | 1.0% Max | 1.0% Max | 0.02% Max [@850°C] |
Characteristics |
|
||
Solubility | Soluble in esters, ketones, aromatic and aliphatic chlorinated hydrocarbons.Insoluble in higehr alcohols | ||
Application/Industry | Used as a reinforcing resin in tire beads, shoe soles, apex strips and co-extruded window profiles. Can be used as an epoxy-phenolic co reactant in wide range of epoxy co reactant applications like laminates, adhesives and coatings Can also be used in varnishes, insulations, inks and coatings |
Low Viscosity Thermoplastic Phenol Formaldehyde Resins
Low Viscosity Thermoplastic Phenol Formaldehyde Resins
POLYTONE® PF 425 and POLYTONE® PF 420 are Non Heat Reactive/Thermoplastic Phenol –Formaldehyde Novolak Resins POLYTONE® PF 420 is a high purity Non Heat Reactive/Thermoplastic Phenol – Formaldehyde Novolak Resin with low softening point. POLYTONE® PF 425 and POLYTONE® PF 420 can be used as an epoxy-phenolic co reactant in wide range of epoxy co-reactant applications like laminates, adhesives and coatings POLYTONE® PF 425 and POLYTONE® PF 420 can also be used in varnishes and inks
Phenolic Resins /Binder/ Reinforcing/Epoxy Co Reactant | |||
---|---|---|---|
POLYTONE® PF 425 | POLYTONE® PF 420 | ||
POLYTONE® PF 420 | Phenol Formaldehyde Resin (Novolak) | Phenol Formaldehyde Resin (Novolak) | |
Type | Non Heat Reactive /Thermoplastic | Non Heat Reactive /Thermoplastic | |
Colour | Pale Yellow/Light Reddish Brown | Pale Yellow/Light Reddish Brown | |
Softening Point (Ball & Ring) | 110 – 120 °C | 80 – 90 °C | |
Free Phenol | 5% | 2% | |
Characteristics |
|
||
Solubility | POLYTONE® PF 425/420 is soluble in alcohols, esters, ketones, aromatic and aliphatic chlorinated hydrocarbons. | ||
Application/Industry | Tyre /Tire Building, Conveyor Belts, Rubber Hose, Rubber Lining, Rubber Mats, Rubber Sheets, Reinforced Rubber, Fabric Lined Rubber, Rubber Adhesives. POLYTONE® PF 425 and POLYTONE® PF 420 can be used as an epoxy-phenolic co reactant in wide range of epoxy co-reactant applications like laminates, adhesives and coatings POLYTONE® PF 425 and POLYTONE® PF 420 can also be used in varnishes and inks |
2 Component Phenol Formaldehyde with Catalyst / Hexa
2 Component Phenol Formaldehyde with Catalyst / Hexa
POLYTONE® PF 200/201 are Non Heat Reactive/Thermoplastic Phenol – Formaldehyde Novolak Resins. These are 2 step resin containing Hexa.
COATINGS: Cured phenolic resins demonstrate exceptional chemical resistance. Railroad cars, storage tanks and heat transfer equipment are coated using phenolic resins as part of baked phenolic coating systems.
COMPOSITES: Phenolic resins are the polymer matrix of choice in composite products especially when meeting high flame, smoke and toxicity (FST) properties. Phenolic resins provide for excellent strength at elevated temperatures in a variety of environments and are compatible with a multitude of composite fibers and fillers. Multiple applications benefit by using phenolic resins in the following composite part manufacturing processes:
REFRACTORY: High carbon yield, wear resistance, and excellent particle wetting and bonding properties make phenolic resins ideal for refractory products.
Phenol Formaldehye Resin/2 Component Resin | |||
---|---|---|---|
POLYTONE® PF 200 | POLYTONE® PF 201 | ||
Chemical Classification | Phenol Formaldehyde Resin with Hexa | Phenol Formaldehyde Resin with Hexa | |
Type | Heat Reactive/2 Step mixed with Hexa | Heat Reactive/2 Step mixed with Hexa | |
Colour | Cremish Yellow | Cremish Yellow | |
Melting Point (Capillary) | 75° C – 90 ° C | 70° C – 85 ° C | |
Inclined Plate Flow @ 125° C | 30 – 35mm | 30 – 45mm | |
Hot Plate Cure @ 150° C | 75 – 100 seconds | 40 – 65 seconds | |
Sieve Analysis (200 Mesh) | 90 - 95% Min | 96 – 99% Min | |
Hexa Content | 9 – 10 % | 7.5 – 8.5 % | |
Free Phenol | 2 % Max | 2 % Max | |
Characteristics |
|
||
Solubility | POLYTONE® PF 200/201 is soluble in alcohols, esters, ketones, aromatic and aliphatic chlorinated hydrocarbons. | ||
Application/Industry | Tires and technical rubber goods use straight phenolic novolac resins as reinforcing agents. Abrasives, Emry Wheels, Composites, Refractory, Cured phenolic resins demonstrate exceptional chemical resistance as coatings |
POLYTONE® |
Wire Enamel
|
Cable Insulation
|
Paints
|
Inks & Varnish
|
Antifreeze Polyamide Inks
|
Spar Coatings Weather Resistant
|
Epoxy Diluents Can Coatings
|
Thermoplastic
|
Thermosetting
|
Composites Refractory
|
Abrasives Emry Wheels
|
Contact Adhesive Rubber Adhesive
|
|
---|---|---|---|---|---|---|---|---|---|---|---|---|---|
AP 108 EL | PtBP Resol | ✔ | ✔ | ✔ | ✔ | ✔ | |||||||
AP 109 EL | PtBP Resol | ✔ | ✔ | ✔ | ✔ | ✔ | |||||||
AP 110 EL | PtBP Resol | ✔ | ✔ | ✔ | ✔ | ✔ | |||||||
AP 120 E | PtBP Novolak | ✔ | ✔ | ✔ | ✔ | ✔ | ✔ | ||||||
AP 1201 E | PtBP Novolak | ✔ | ✔ | ✔ | ✔ | ✔ | ✔ | ||||||
PF 132 | PF Novolak | ✔ | ✔ | ✔ | ✔ | ✔ | |||||||
PF 420 | PF Novolak | ✔ | ✔ | ✔ | |||||||||
PF 425 | PF Novolak | ✔ | ✔ | ✔ | |||||||||
PF 200 | 2 Part PF Novolak | ✔ | ✔ | ✔ | |||||||||
PF 201 | 2 Part PF Novolak | ✔ | ✔ | ✔ |
POLYTONE® Range of Phenolic resin has a wide array of application across industries. The reactive phenolic resins finds in application applications like laminates, adhesives and coatings, Modified Phenolic Novolak like the POLYTONE® AP 120E 1201E are used in varnishes, insulations, inks and coatings
- POLYTONE® PF 425 and POLYTONE® PF 420 can be used as an epoxy-phenolic co reactant in
- Wide range of epoxy co-reactant applications like laminates, adhesives and coatings
- POLYTONE® PF 425 and POLYTONE® PF 420 can also be used in varnishes and inks.
- Tires and technical rubber goods use straight phenolic novolac resins like POLYTONE® PF 132/1321 as reinforcing agents.
Cured phenolic resins Iike 2 component PF 200 and 201 demonstrate exceptional chemical resistance as coatings , Abrasives, Emry Wheels, Composites, Refractory.
- Available in 25Kg HDPE Line KRAFT Paper Bags with Anti-Static Liner or 25Kg HDPE Bags.
- Choice of ISPM 15 Standard Heat Treated/Fumigated Pallets or Plastic Pallets.
- Individual pallets must NOT be double stacked – pastilles/lumps are likely to agglutinate.
- Properties are not affected by agglutination.
- Phenolic Resins tend to discolor over time.
- Can be stored up to 12 months at temperatures below 35 °C.
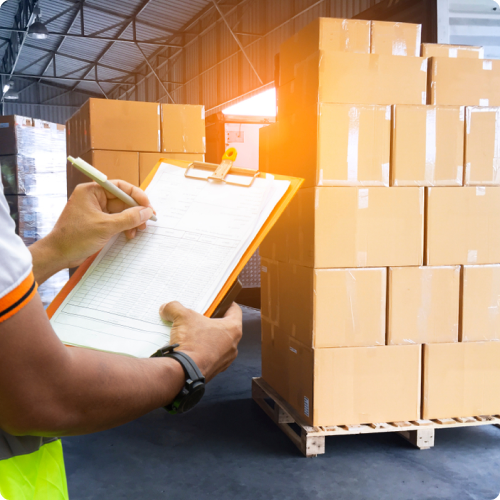
Please follow advice and information provided in MSDS. Protective clothing & workplace hygiene measure must be observed at all times.
Detailed MSDS available on request.
Want to Know more!
Get in touch with our experts!!
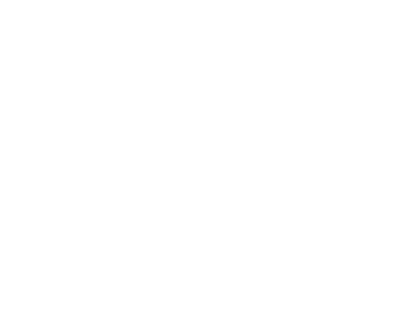
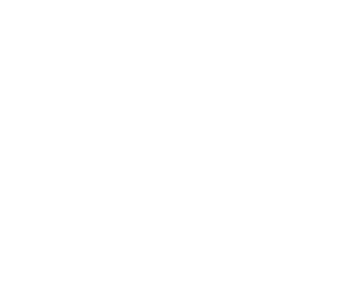